- What is Star Delta Starter?
- What is Automatic Star-Delta Starter?
- Block Diagram
- Components of Induction Motor Timer (Starter) Using Auto Delta Star Starter
- Construction of Induction Motor Timer (Starter) Using Auto Delta Star Starter
- Project report of Induction Motor Timer (Starter) Using Auto Delta Star Starter
- Innovative Perspectives (Future Scope)
- Conclusion
Induction motors are commonly used in industries and typically burn up upon starting.This project is intended to provide induction motors with low voltage starting.
This is accomplished by converting stars to deltas. In 50 Hertz industrial motors, Star/Delta starters are likely the most common reduced voltage starters. Star-delta is utilised to reduce the starting current applied to the motor, after which the full load current is applied.
Since the current in each phase of a star connection is identical, the line voltage is the square root of three times – the phase voltage.
If an induction motor is being started as a star, the voltage is reduced. In a delta connection, the voltage is the same as the phase voltage, so the entire voltage is applied when the motor is operated in this configuration.
This project involved the design of an automatic star-delta ignition using electrical relays & an electronic timer.
By supplying the motor with 58% of the full load current to limit the starting current fluctuations caused by starting the motor at a reduced voltage and then reconnecting the full supply voltage when the motor has reached near-rotational speed.
This technique is generally known as “Soft starting” the motor.
What is Star Delta Starter?
Star-Delta starters have the lowest voltage in the 50 Hz frequency (or) 60 Hz depends on location.
They are used to minimise the start current provided to the motor at startup in order to prevent electrical supply disruptions and interference.
The electrical connection from the power source to the motor is connected from the star to delta in the star-delta starting method.
The motor requires 58% less voltage when connected in a star configuration. Yet, since torque is proportional to the square of voltage, the initial torque decreases.
The drawback of employing star-delta starting is the large decrease in motor starting current, which results in significant cost savings for
- Cables,
- Transformers, and
- Switchgear.
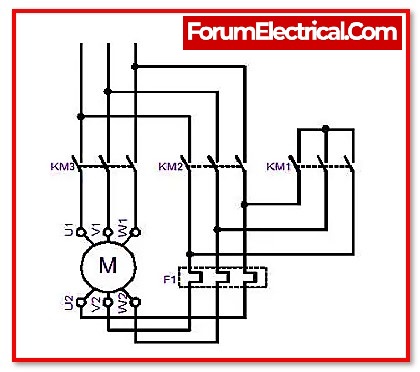
What is Automatic Star-Delta Starter?
Because of the shortcomings of the above starting methods, further study is required to correct these problems.
As a result, automated star relays and an adjustable electronic timer were constructed.
The automatic star starter uses more advanced hardware and software components than the native star, and it also corrects the current surge problem of open transition starting by using an additional contactor and a set of resistors to maintain the motor on transition, which is known as closed transition.
Block Diagram
Components of Induction Motor Timer (Starter) Using Auto Delta Star Starter
1). Hardware specifications
- Relay
- 300 Relays
- 1C/O Relay
- Transistors
- Capacitors
- Transformers
- 555 Timers
- Resistors
- LEDS
- Diodes
- Lamps
2). Software specifications
No requirements of any software.
3). Power Supply
In order to provide a three-phase supply, the power supply block features three single-phase transformers and a diode bridge rectifier dedicated to each of the single-phase supplies.
Both the timer and the relay coils will be driven by the output of the diode bridge rectifier.
4). Timer
The motor may be switched from a star connection to a delta connection by using a timer.
It is able to make adjustments to the time period for switching transition based on the fluctuation in the potential meter.
5). Relay
In order to accomplish the switching in response to the various conditions, this circuit’s implementation utilises a total of four relays.
In addition to that, these relays protect the motor from single phasing.
a). 300 Relay
The 300 series of relays Power Relays provide high amperage DPDT performance in a device that can be mounted using a conventional flange.
When coupled with the blowout magnet function that is available as an option, the Relays 300 series is constructed for high voltage DC (or) AC switching.
b). 1C/O Relay
1 C/O Pluggable and replaceable relays are included in the relay module.
Indicator LEDs located at the output, together with a signal for card identification and able to withstand high temperatures and stress, as well as being DIN rail mountable.
It is afree-wheeling diode across relay coil which is perfect for conditions in which the temperature is constantly changing.The capability to route inputs through flexible jumpers.
Construction of Induction Motor Timer (Starter) Using Auto Delta Star Starter
The contactors & an adjustable timer that comprise a star-delta starter are that allows an induction motor to be started in star mode.
The timer then determines when it is the right time to turn the motor over to delta mode after a certain amount of time has passed.
The project makes use of three step-down transformers, the primaries of which are connected in star mode, while the transformers’ secondary windings generate filtered dc after passing through their respective bridge rectifiers and filter capacitors.
Of the three such dc (direct current) derived, one dc is used for a timer circuit constructed around a 555 timer connected in astable mode and yet operating in mono stable mode.
The two relays are controlled by two additional dc supply. These two are connected together in series with third relay coil that is linked to them.
The three phases’ mains are linked to the third relay in this configuration. The fourth relay is responsible for the conversion from star to delta.
The timer is responsible for operating this fourth relay. Single phasing refers to the absence of either one (or) two phases Y and B, and requires the use of either relay.
Relay 1 or relay 2 to an off state, which will cause relay 3 to turn off.
The motor is started as a star connection due to the connection of the 4th relay in star at the starting condition.
When a certain amount of time has passed, the timer will begin to activate the 4th relay coil, which will cause the relay to flip to the delta mode.
In addition to this, it displays via LED the mode in which the motor is now functioning.
Project report of Induction Motor Timer (Starter) Using Auto Delta Star Starter
This project makes use of a system that can start a three-phase motor at 440 volts AC mains supply at 50 hertz using a series of relays in star connection at first, and then an electrically controlled timer can switch them over to delta mode.
In order to change the motor connections from the star to the delta while maintaining the time delay, a series of relays is used.
In place of a three-phase motor, this undertaking is supported by six lights; specifically, each of the three windings of the motor is represented by a pair of lamps.
To ensure that the starter may be securely operated while it is being used, the inter-locking arrangement of the relay coils & the electronic timer are all linked to a low voltage and are supplied with power from an internal DC power source.
It is still applicable for starting a three-phase motor and also prevents single phasing from occurring.
During star operation, the lights would burn dimly, which indicated that the supply voltage all across coils was decreased by the root three factor.
When the timer has been activated in a delta condition, the lights will glow with full intensity, indicating that the supply voltage is at its maximum.
The timer is set to operate in mono-stable mode, and its output is connected to a relay that modifies the mains supply so that it is now three-phase delta rather than star.
This timer is operated by the DC power source that has been controlled.
This project also involves the inclusion of single-phasing protection in order to prevent against the burning out of three-phase motors in the event that any one phase fails while the motor is operating.
In the condition that there is a phase failure, the output that is delivered to the lights must be totally turned off.
Innovative Perspectives (Future Scope)
As compared to the methods that use lower voltage, this method is the easiest and most cost-effective way to start the motor.
Moreover, during switching operations, it needs a significant quantity of rush current.
The project might be improved further by using thyristors in firing angle control mechanism for soft-start of the induction motor.
This would solve all of the problems that are associated with employing a star delta starter.
Conclusion
This method of starting is used for motors that operate on low to medium voltage & have a low starting torque.
It is the most cost-effective method for lowering the starting current, which in the case of direct online (DOL) starting of an induction motor may be as much as three to four times higher.
The relays & the timer circuit should have no trouble carrying out the implementation.
The method in which the relays are connected serves to protect the motor from operating in single phasing.